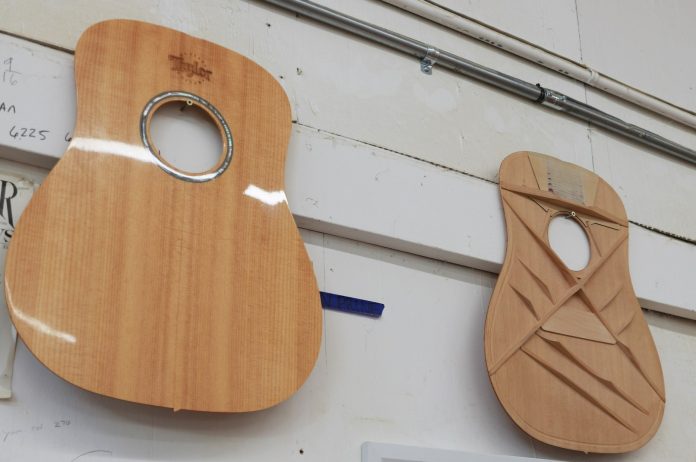
If you own an acoustic guitar, you might wonder where its wood came from. For almost anyone owning a Gibson, Martin, or Taylor brand acoustic guitar, the answer might be a little closer to home than you expected. Pacific Rim Tonewoods, a specialty sawmill located off State Route 20 about 16 miles east of Sedro-Woolley, processes between $4 and $10 million dollars annually in spruce, maple and koa wood for instrument manufacturers big and small.
Wood that passes through Pacific Rim is primarily used for soundboards—the top portion of an acoustic guitar that’s heavily responsible for the instrument’s tonal quality—as well as the sides, backs, binding, and bracing of guitars, ukuleles, and other wooden instruments.
The mill was founded by Steve McMinn, a former wood shop teacher at Western Washington University who became intrigued by tonewoods in the 1980s. McMinn started what would become Pacific Rim by salvaging blown down spruce logs and milling them inside his home garage.
In 1992, McMinn re-located his growing business to Birdsview, the tiny Skagit River hamlet located about halfway between Hamilton and Concrete. Settling at the site of a former shake mill, Pacific Rim has grown slowly but steadily in both operations and client base. Its more than 30 employees are driven by a desire for quality and innovation in the products they provide luthiers across North America, Australia, Asia and Europe.
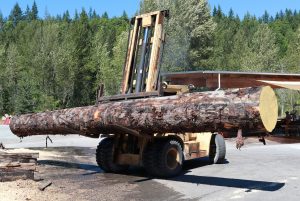
“I like projects,” says McMinn. “I like problem solving. I like making beautiful things with wood. But I like making jobs, too, that pay well and are interesting, because I think it’s important.”
One of those jobs belongs to Eric Warner, Pacific Rim’s general manager. Warner began there as a janitor in 1994, when there were only about seven employees. From the milling process to the meticulous nature of their research projects, Warner says Pacific Rim takes the visual and auditory quality of their lumber very seriously.
“Everybody’s proud to work here, and to contribute to the acoustic guitar,” he says. “Which, in the end, contributes to a lot of the music that’s being created. There’s a lot of pride in ownership for everybody that works here.”
The Process
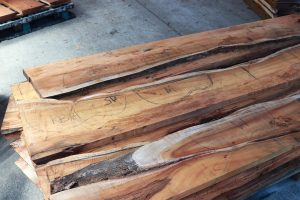
A guitar top’s journey into existence begins, of course, with the trees they come from.
The bulk of Pacific Rim’s business is done with spruce trees, sourced primarily from up and down the British Columbia coast. Western big leaf maple, sourced more locally in Whatcom and Skagit counties, and elsewhere in Western Washington, makes up another substantial part.
The business also imports koa from Hawaii, and uses smaller quantities of woods like ebony and rosewood for manufacturing components of body, fretboard or peghead binding.
Pacific Rim finds its raw products by visiting log sorts or log yards, selecting individual trees with the end product of good instruments in mind. Once selected, logs are taken back to Pacific Rim and stored in the cool cover of the forest behind the facility, with additional steps taken to prevent spoilage. “Trees are like giant vegetables,” Warner says. “As soon as they’re harvested, they’re going to want to rot and decay and decompose.”
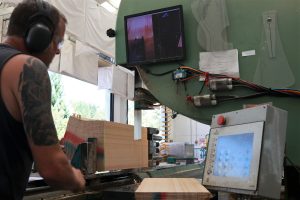
When it comes time for processing, logs are cut into 22-inch rounds (roughly the height of a guitar), which are then gradually sawed down into smaller and thinner pieces until they reach the final size of a soundboard blank. These blanks are then sent to the instrument manufacturer, who shapes the wood into the actual instrument.
Much like professional baseball players who visit the Louisville Slugger factory to select wood for their bats, luthiers for most of the major guitar companies have visited the facility to select wood.
Pacific Rim produces nearly 300,000 soundboard blanks annually, and the process of creating them is an amalgamation of physical labor and a scientific understanding of wood properties and their relation to sound, strength, and appearance.
Each piece of wood is graded, dried and then stored before being shipped. On property are several kilns—including a vacuum kiln and a European-designed autoclave—which use extremely high temperatures and pressures to expedite the drying process.
Beyond the Cut
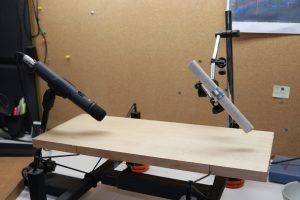
Pacific Rim also has a wood laboratory: a place where the stiffness, damping and density of milled boards can be compared, and acoustic profiles given to luthiers. In one part of the lab, a piece of wood sits with two microphones just above it. Dropping a marble on the board allows them to measure the wood’s dampening properties, Warner says.
The facility also includes an engineering room, as well as several maintenance rooms. The mill’s abundance of metal band saws require constant sharpening on computer numerical control (CNC) machines.
Warner says Pacific Rim also strives to be as sustainable as possible with its wood usage: if a piece is found to be defective or inferior for a guitar top, it may be used for something else, such as bracing.
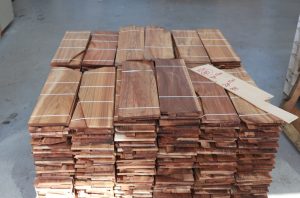
Besides providing their employees with good wages, much of Pacific Rim’s income is re-invested into research that has the opportunity to help shape the future of both wood harvesting and instrument manufacturing. Among their projects are collaborations with scientists and guitar manufacturers, including on subjects like spruce soundboard grading, thermal modification of tonewood, and the genetic propagation of instrument-preferred maple trees.
So the next time you pick up an acoustic guitar, realize that the process used to create it might have started right here in the Skagit Valley.